We are sustainability enablers
We have long recognized that social and environmental responsibility must be an integral part of our overall business strategy. We implement a corporate responsibility strategy that focuses on 5 major areas of action.
Cover Image
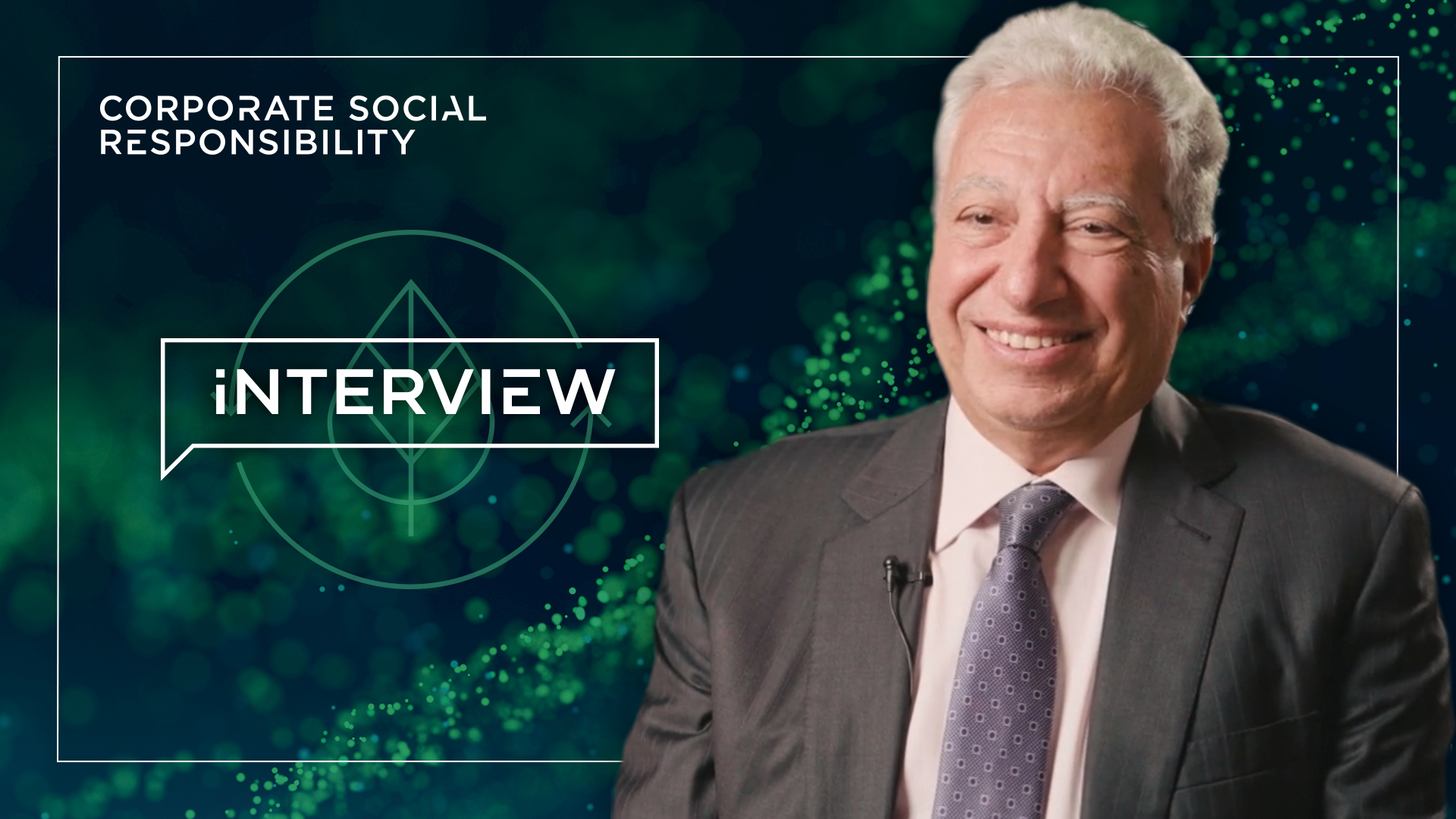
Video file
Lectra's key sustainability commitments

Respect the highest ethical standards
We lead by example and take our responsibilities seriously by adhering to the strictest ethical standards.

Design eco-responsible offers
We help our customers minimize their environmental impact while implementing Industry 4.0 principles, primarily by reducing material consumption.

Promote an inclusive, diverse, and vibrant work culture
We offer a safe work environment where employees from around the world can reach their full potential, find fulfillment, and contribute to society.

Reduce our environmental footprint
We are committed to a sustainable and resilient industrial-model by working constantly to minimize our environmental impact, including for our newly acquired companies.

Provide support for the next generation
We are committed to training the next generation of fashion professionals by sharing our knowledge, expertise and solutions to develop their skills and employability.
At Lectra, we are committed
We have built our business on a foundation of integrity, employee well-being and continuous innovation with a focus on environmental sustainability.
Learn more on how we deploy our corporate responsibility strategy through our key sustainability commitments.
Learn more on how we deploy our corporate responsibility strategy through our key sustainability commitments.

Sustainability awards

Ecovadis
Lectra received the Silver medal by Ecovadis. Our overall score of 70/100 places us in the top 10% of all rated companies and showcases our commitment to continuous improvement.

EthiFinance ESG Ratings
Lectra is awarded gold level recognition by EthiFinance ESG Ratings in 2024 (based on 2023 data) with a clear improvement on 2023 to 79/100, i.e., +5 pts.
What our customers say
Ovidijus Jalonskis
CEO, Vilmers
Lectra offers digital solutions to help customization and modularity in production
Felix Lopez Gil
FAMA’s CEO
We went from making straight sofas to playing with curved shapes; it opened up an incredible world of possibilities. It also gave us the opportunity to make an impressive leap in quality.
Latest resources about sustainability

Fashion
Product-related articles

Automotive
Customer stories

Furniture
Trends & insights

Lectra
Trends & insights

Lectra
Trends & insights

Furniture
White papers

Fashion
Product-related articles