Tesca Group improves performance at overseas facilities with Automotive Cutting Room 4.0
Using powerful automated monitoring and analytics, the automotive seating and interior supplier can now access actionable data in real time to make critical business decisions at remote locations.

A premier manufacturer of high-end seating systems
France-based Tesca first began manufacturing textiles in 1836. The family-run business designs and develops technically advanced vehicle seating and interior components that emphasize passenger comfort and safety. Now a major supplier of high-end automotive interiors, the company crafts each model with utmost precision, from its Paris design studio to production lines worldwide. As the partner of premium carmakers, Tesca aspires to the same level of creativity and innovation. Today a global automotive supplier, Tesca operates 21 locations and 16 production sites worldwide, backed by a workforce of 3,500 employees
The need for performance monitoring across plants
With an installed base of 12 Vector fabric cutters, Tesca is a long time Lectra customer. Late in 2019, Tesca’s operations management team turned to Lectra to help resolve inefficiencies that were hampering production. To review reporting and launch improvement initiatives, Tesca’s operations management team needed to be able to analyze large data sets faster and more efficiently. Because Tesca’s local manufacturing facilities report performance indicators using different metrics, corporate decision-makers also needed to establish comparable KPIs. The customer also sought to standardize processes in the aim of improving productivity and machine availability, as well as shortening response time in the event of stoppage.
Algopex Continuous Improvement Enabler
To bring Tesca’s manufacturing base up to the Industry 4.0 standard, Lectra recommended that the company implement its Automotive Cutting Room 4.0 solution to harmonize reporting methodologies, measurements, parameters, and best practices across manufacturing facilities. Designed to digitalize cutting room workflow, the visionary new solution combines cloud-based software, enhanced equipment capabilities, scalable customer success services, and advanced analytics for data-driven decision support that optimizes manufacturing performance.
Automotive Cutting Room 4.0 comprises Valia Preparation & Planning Manager, Empower Next-Generation Services, and Algopex Continuous Improvement Enabler. The solution helps customers derive more value from their Vector cutting lines by gaining insight from production data. Since Tesca’s implementation of Automotive Cutting Room 4.0’s Algopex component at plants in Morocco and Tunisia, Tesca now has a real-time monitoring system that allows local teams to respond as soon as issues arise, limiting downtime and process disruptions. When a KPI exceeds a defined threshold, an alert is sent to the cutting room manager. Custom settings also enable alerts to be escalated to the plant managerial hierarchy.
Faster, more efficient data retrieval and analysis
Alexandra de Oliveira, Innovation Leader for Cut and Sew and Leather Manager, Tesca, plays a key role in coordinating the first two Tesca facilities to implement Algopex. “In my role, I need data to monitor the performance of the cutting room and coordinate improvement initiatives with the plants,” explains de Oliveira. “We have vast amounts of data, but what I needed was actionable information to focus analysis on areas with the highest improvement potential and maintain that performance over time. Before, it took a long time to retrieve and analyze cutting room data. With Algopex, I can really accelerate the process.”
An optimized manufacturing process is key to succeeding in an environment as competitive as the automotive interiors industry. According to de Oliveira, Algopex makes it easier to identify, define and launch improvement initiatives with the teams in the plants.
“Algopex enables us to visualize specific KPIs and track the impact of continuous improvement measures” continues de Oliveira.
“For each KPI, an industry benchmark is provided together with a first evaluation of potential savings. From this level, it’s possible to drill down into more detailed facts and figures, including a Pareto analysis.”
Watch our interview with Tesca’s Alexandra de Oliveira
Cutting Room 4.0 provides our operators, team leaders and managers with the visibility they need to work together to improve performance KPIs. All of them can participate in the identification and implementation of the actions to achieve the goals.
Alexandra de Oliveira
Innovation Leader for Cut and Sew and Leather Manager, Tesca
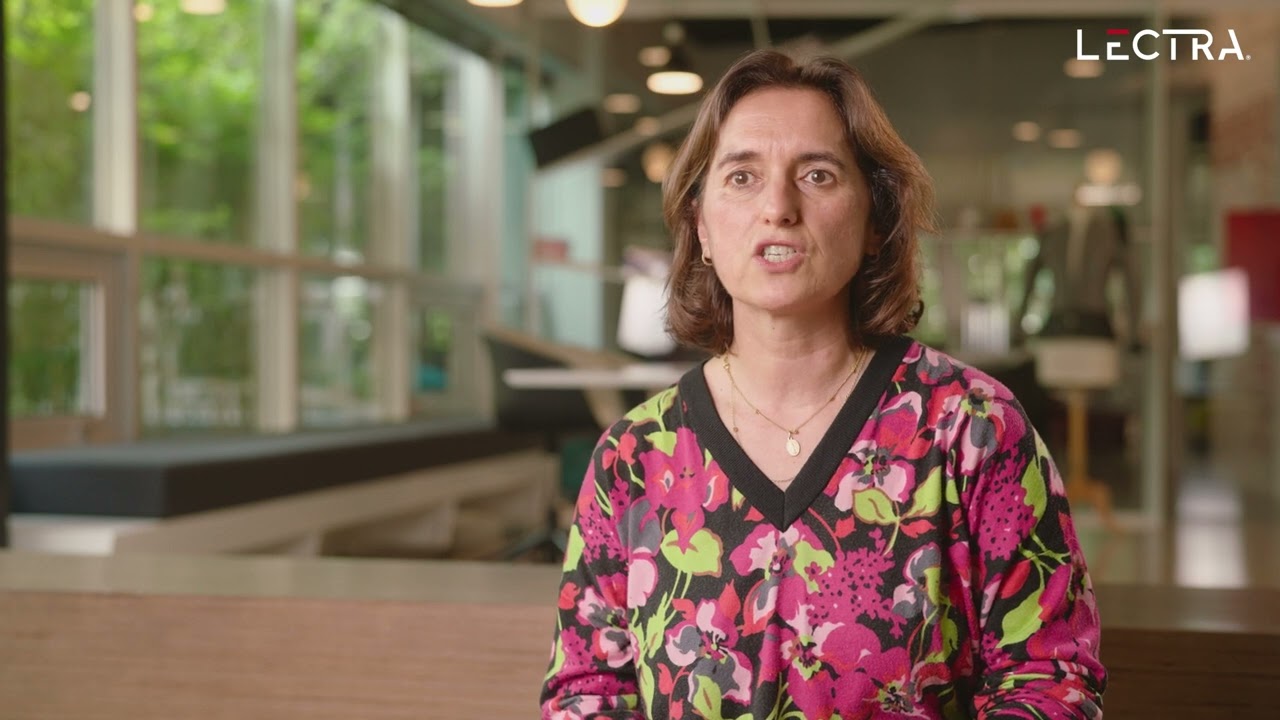
Digitally managed performance improvement
Since the implementation of Algopex, Tesca has already observed a 3.5% reduction in raw materials and 2% increase in cutting capacity at the two facilities.
"At Tesca, we're convinced that the real-time monitoring, analytics, and performance improvements enabled by digital transformation are essential to adapting operations to our business environment,” observes Renaud Cellier, Deputy Director, Covering Materials, Tesca.
“Algopex was exactly what we were looking for. It’s important to remember that production is always changing. In addition to new programs, we also receive revised product specifications from customers. We introduce new materials. We have new operators joining the company and new plants to ramp-up. All of these changes must be monitored and managed with a continuous improvement-oriented approach that’s now simplified by Algopex.”
Following the initial successful implementation of Algopex at its production plants in Morocco and Tunisia, Tesca Group has signed to implement Algopex in Portugal and Mexico, with tentative plans to deploy Automotive Cutting Room 4.0 more broadly in the near future.
Watch our interview with Tesca’s Renaud Cellier
We have already achieved improvements in a short period with ALGOPEX – a 3.5 % reduction in raw materials and 2% increase in cutting capacity. These figures already demonstrate the benefits, but the most important functionality is the possibility to monitor the results achieved after implementing the improvement actions.
Renaud Cellier
Deputy Director, Covering Materials, Tesca
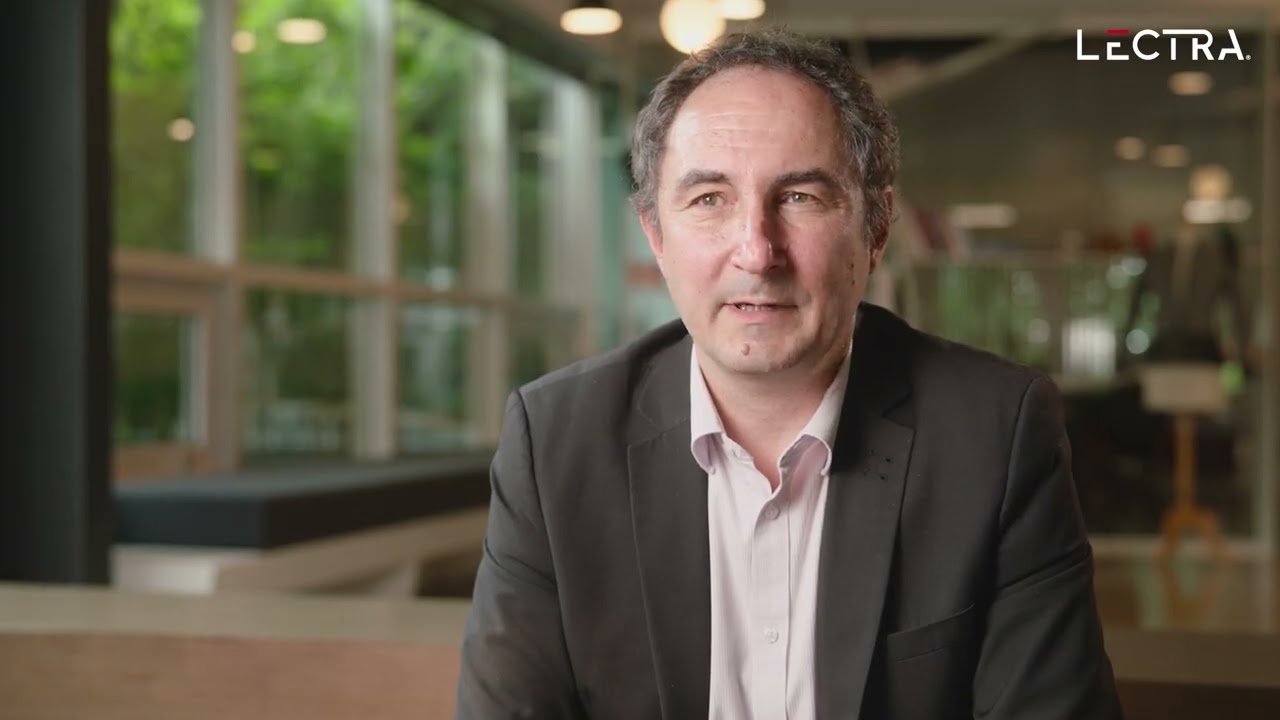
Discover Lectra's solutions implemented to help Tesca Group improves performance
Related Content



