Nalesso’s productivity increases by 15% with Lectra
Furniture On Demand by Lectra has helped the family-owned business achieve its productivity and material-savings targets
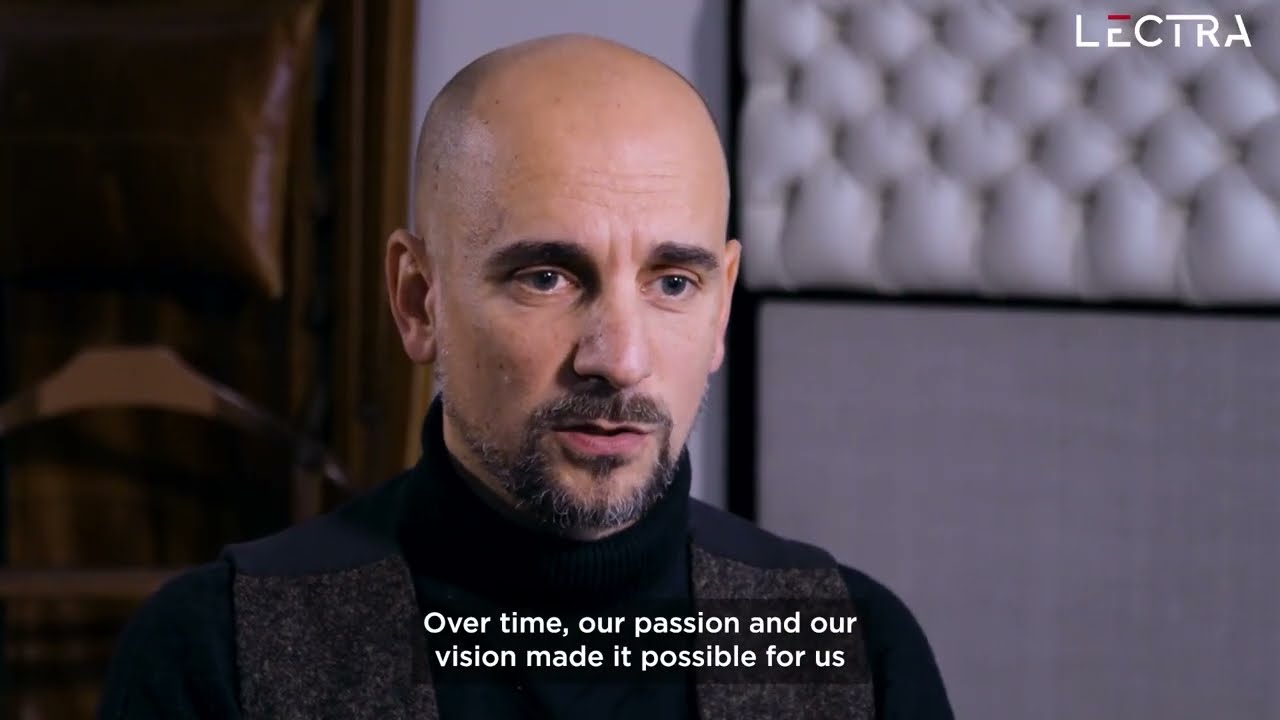
A cutting-edge company in custom-made furniture
The company was founded in the 80s by Armando and Dina Nalesso as a small artisan workshop and, in 40 years, it has grown by focusing on custom-made products, expertise and a relentless quest for technical materials.
Today, it is a well-established Italian company within the segment of custom-made indoor and outdoor furniture and it partners with the most renowned luxury brands and internationally acclaimed architects.
From order to delivery, Nalesso's product management process aims at understanding the customer's needs and fulfilling them. For each item, the right materials are selected and all stages of production, logistics and after-sales are closely monitored.
Nalesso is able to manufacture a single prototype, as well as small series or dozens of items with different materials and different timelines.
Furniture on Demand by Lectra
Read other testimonials about Furniture On Demand with Valia
Adam Schindler
Ovidijus Jalonskis
Felix Lopez Gil
Related content






